There are different types of formwork available for different purposes. Generally, the formworks for vertical concreting are called wall forms and those for horizontal concreting are called slab or floor forms. The various types of formwork available today in the market are discussed in detail.
Traditional Formwork
- This usually consists of standard framed panels tied together over their backs with horizontal members called waling.
- The waling is provided with the basic function of resisting the horizontal force of wet concrete.
- One side of the wall formwork is first assembled ensuring that it is correctly aligned, plumbed and strutted.
- The steel reinforcement cage is then placed and positioned before the other side of the formwork is erected and fixed.
- Plywood sheet in combination with timber is the most common material used for wall formwork.
- The usual method is to make up wall forms as framed panels with the plywood facing sheet screwed on to studs on a timber frame.
- This allows for the plywood to be easily removed and reversed and used on both sides so as to increase the number of reuses.
- The wall forms are susceptible to edge and corner damage and must be carefully handled.
- Special attention must be given to comers and attached piers since the increased pressures applied by wet concrete could cause the abutments to open up, giving rise to unacceptable grout escape and a poor finish to the cast wall.
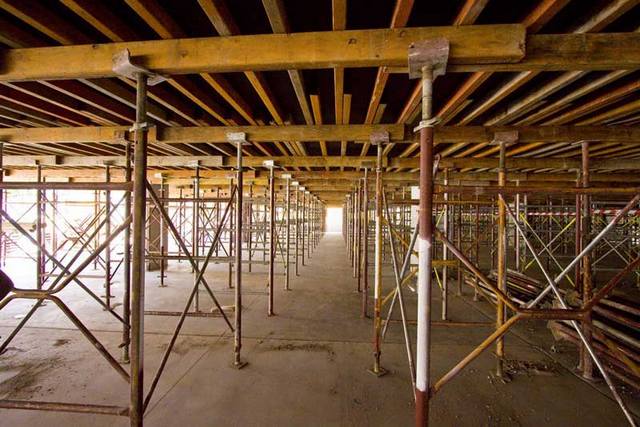
Climbing Formwork
- Method of casting walls consists of a climbing formwork, the climbing of which may be manual or crane assisted.
- It employs a common set of forms used in a repetitive manner for casting walls in set vertical lifts.
- After each casting the forms are removed and raised to form the next lift until the required height has been reached.
- These forms are widely used in the construction of industrial chimneys, silos, high rise towers & building cores, bridge piers & pylons, airport control towers, telecommunication, towers etc.
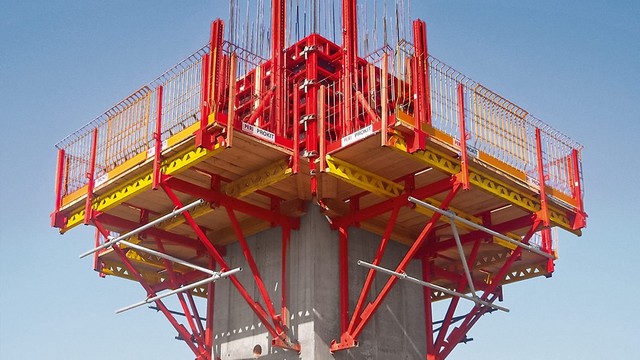
Advantages of Climbing Formwork
- Staged construction process allows balance of site resources.
- Anchor accessories can be reused after each pour, reducing material costs on current and future construction programs.
- In case of trolley mounted formwork, the panel retracts from the face, providing space for cleaning and fixing of concrete.
- Formwork & access platforms lifted as one, minimizing crane support, reducing labour and material costs.
- Fine adjustments of the form face can be made during construction, providing accurate alignment of the form face vertically & laterally.
Sliding Formwork or Slipforming
- Slip form means a continuously moving form, moving with such a speed that concrete when exposed has already achieved enough strength to support the vertical pressure from concrete still in the form as well as to withstand lateral pressure caused by wind etc.
- Thus, the slip form concreting technique is a rapid and economical construction method that can be applied with great advantage to many types of construction projects such as chimneys, silos, water towers, bridge-columns, lift shaft cores and shaft lining etc.
- The technique is based on movable forms which are gradually lifted by hydraulic jacks.
- It is a continuous process where wet concrete is added to wet concrete.
- Reinforcing steel and/or post tensioned cables are continuously fixed as the normal slipping speed is 3 to 6 meters per 24 hours.
- The slip form construction is designed for each project depending on the structure of the project.
Advantages of Slip Forming
- Minimum consumption of timber and steel plates.
- Total elimination of traditional scaffolding
- Minimum requirements of carpenters for assembling.
- It gives a monolithic structure.
- The concrete surfaces can be treated and finished while concrete is green.
- Depending on the weather conditions, it is possible to achieve a vertical rise to the tune of 4 to 5 m in summer and 2 to 3 m in winter.
- The procedure of continuous slipping is applied to making both inner and outer walls as well as columns of a building.
- Form climbs.
Permanent Formwork
- Permanent form or stay-in-place formwork is one in which the form is left as an integral part of the structure.
- Permanent formwork can also be utilized as the facing materials of in situ reinforced concrete.
- They can be of two types—participating and non-participating.
- The material used for these forms must be durable and of sufficient strength.
- Commonly used materials include polyvinyl chloride (pvc), galvanized coiled sheet steel, fabricated steel, carbon/epoxy thin shell.
- The high initial cost of design and installation, lack of familiarity for installation and maintenance and more specified form design are some of the barriers to the use of this form.
- However, there are various advantages like low cost of transportation and installation, precise form design, maximum flexibility, greater durability with reduced long term maintenance and versatility.
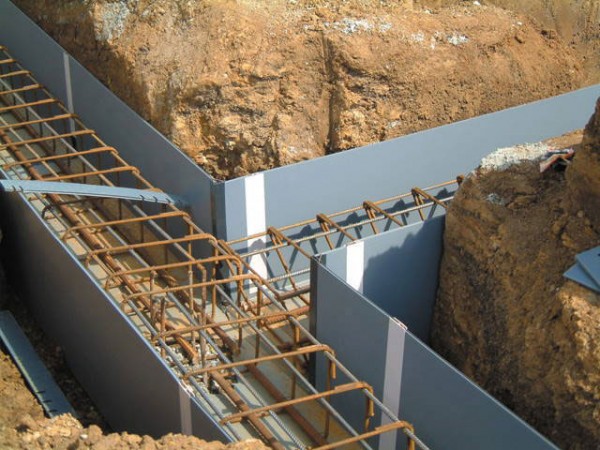
Special Forms
These are those forms that are specially designed and manufactured for a particular kind of construction. The need for a special formwork may arise due to several factors such as :
- When the contract demands the highest class of dimensional tolerance to be followed.
- Where the form work shape required becomes uneconomical or impracticable for site fabrication.
- Where the formwork is required to be self-contained i.e. self propelled,
- Where rate of concreting, admixtures or types of concrete are such that concrete pressure developed within forms and stresses in the forms demand special attention where a substantial number of re-uses is envisaged.
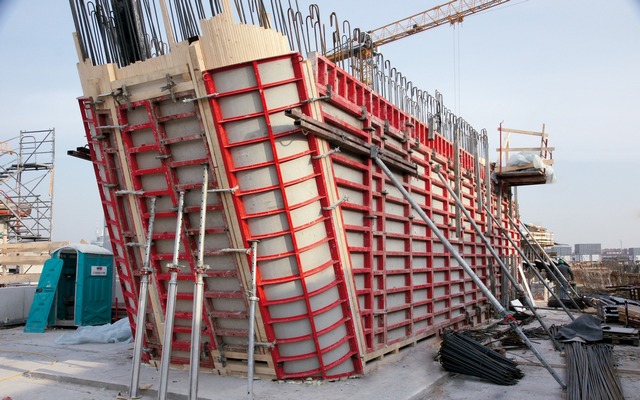
Table Form
This is a special formwork designed for use in casting large repetitive floor slabs in medium to high-rise structures. The main objective of reducing the time required re-erecting, striking and re-erecting slab formwork. A system which can be put as an entire unit, removed, hoisted and repositioned without any dismantling.
Ganged Panel Form
The increasing pace in the construction of multi-storey and massive concrete structures, and the parallel progress in development of cranes and other mechanical methods of transporting forms have made the use of ganged prefabricated forms for the concreting of large sections of high walls very common.

Ranging up to 30×50 ft, their size is limited only by the mechanics of handling. Large panels can be assembled flat on the ground where it is easier to work. Delay and lost motion are avoided in stripping because the gang forms are stripped as a unit.
Tunnel Form
The tunnel formwork is a room sized structural steel fabricated form which is used to cast the RCC walls and floor slabs of a building as a monolithic structure in a continuous pour. The forms are then heated using hot air blowers for accelerated curing of the concrete. This system is most economical when the structure consists of large number of identical units.
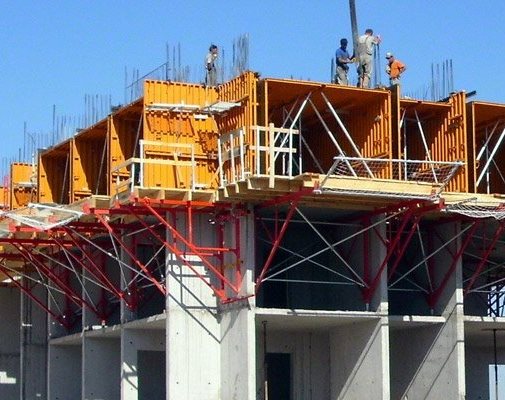
There exist two versions of this type of formwork. They are:
- The half tunnel formwork used to cast only one wall and slab simultaneously.
- The full tunnel formwork used to cast two walls and a slab simultaneously.
The sequence of construction involves :
- Placing of reinforcement, electrical and sanitary conduits along with the tunnel forms.
- Concrete is then poured and the open side of the forms is covered and hot air blowers placed inside.
- The forms are removed the next day and placed on the next site using cranes.
The optimum use of tunnel form is in multiunit shear wall structure with identical floor layout at each level.